We at Creative Fields care about future generations, seeing them as potential future co-workers so we do our best to help them educate and prepare them for all the challenges of today’s and tomorrow’s labour market. Therefore, in the spring of 2015, we donated our software licence to the students’ association FSB Racing team. They have used it in the process of simulating their racing car. A few months later, the boys contacted us saying how satisfied they were with our products. Here is what we talked about one foggy morning at our office.
What were your main assumptions when you started simulating your racing car?
Even though the average cornering speed at Formula student events is not significant when compared to other competitions, numerous lap time simulations have revealed to us that the loads created by the motion of the air are important, and utilizing aerodynamics significantly improves performance even within such a speed range.
However, it also brings some negative effects with it, like increased drag, higher centre of mass and overall weight increase. Our main objective was to minimize negative effects and fully utilize positive effects.
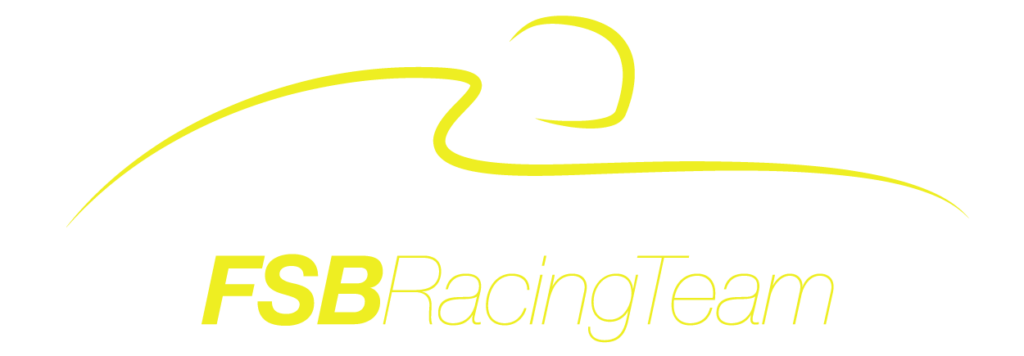
How did you solve the difficulties you faced with?
Drag can be reduced by minimizing flow separation, and having a smooth external surface. These were the main objectives of the car body design. An undertray with a rear diffuser was considered.
However, due to its nature of high sensibility to the transient motion of the vehicle, and taking into consideration previous research and testing, it is concluded that the downforce produced with such a method is not worth the weight increase when compared with the downforce gained from wings. Therefore, multi-element front and rear wings were designed to produce downforce. Even though the competition rules allow some radical designs, our objective was not to get huge downforce values without taking into account negative effects such as drag, weight increase, manufacturing complexity and cost. The main objective was to achieve reasonable values of downforce from the simple aero package. We examined various combinations of airfoils interaction using 2D CFD simulations to get the most favourable setup.
Afterwards, we proceeded with in-depth 3D simulations of the whole car to further optimize the performance of the aero package. Small corrections were made possible for on-track testing to evaluate simulation results and further optimize driving behaviour.
How have cfMesh and CF-MESH+ helped you in your work?
In the process of setting up CFD simulations (both 2D and 3D), mesh generation was often the most time-consuming step that required a great effort to produce a high-quality mesh. CF-MESH+ proved to be an easy-to-use and robust tool for the preparation and execution of CFD simulations within the OpenFOAM framework.
While preparing 2D simulations, the automatic mesh generation tool cfMesh saved us a lot of time and effort by giving us the possibility to generate high-quality meshes for hundreds of various airfoil configurations in just a few clicks.
What kind of options from cfMesh and CF-MESH+ did you find most useful?
In preparation for 3D simulations, numerous options proved to be very useful.
The “feature edge” option enables us to treat specific edges as sharp features that are constrained by the mesher in order to preserve geometries of great importance. The “Keep cells intersecting boundary/patches” option was very useful while meshing small gaps between wing elements, which can also sometimes cause significant geometry distortion. The new “optimiseLayer” option significantly increases the quality of boundary layers, which is very important for near-wall treatment. While visualizing the geometry inside CF-MESH+ the option for cell size preview is especially nice for sparing the user from the often annoying “trial and error” method in the automatic mesh generation process.
From our experience, CF-MESH+, being a GUI driven tool, makes the learning process much easier for students that have no experience with OpenFOAM and are not familiar with terminal (no GUI) environments.
Robert Keser, FSB Racing Team member